Separator milk cleaner MAXCREAM
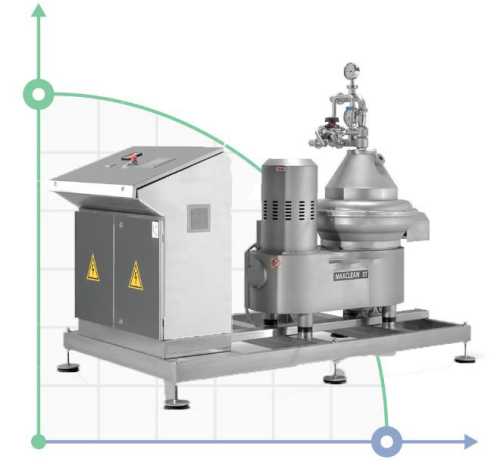
Separator milk cleaner MAXCREAM
The MAXCREAM separator is a centrifugal separator designed specifically for use in the dairy industry. It is equipped with two pressure chambers with discs, partial and full automatic unloading functions and is also suitable for CIP cleaning. MAXCREAM is supplied as a separate unit mounted on a frame and equipped with its own control cabinet.
Application
- MAXCREAM separators have been developed by HAUS for the dairy industry, in particular for milk or whey. Their purpose is to separate fatty components from milk or whey, while removing mechanical impurities. MAXCREAM separators separate into:
- Milk or whey with a reduced fat content (standardization) purified from mechanical impurities.
- Cream of a given fat content.
- Sludge consisting of solid impurities.
MAXCREAM separators are both effective in reducing somatic cells and spores.
Capabilities
The MAXCREAM separator belongs to a new generation of separators and is designed exclusively for dairy products. It achieves the maximum level of efficiency, at the same time with gentle processing and high hygiene. Thanks to advanced features, effects are achieved:
- High rotation speed: generating large centrifugal force due to quality material and mechanics.
- Special plate pack: densely spaced large diameter plates creating a large separation surface.
- Specially Designed Feeding Tube: A system that allows gentle feeding and dispersal of product, minimizing shear, air entrapment and foaming.
- Discharge system with two valves: able to discharge quickly and accurately, reducing the loss of milk and its valuable components (fat, protein).
- Two pressure discs, constant pressure valve and outlet valve: to regulate the separation process and obtain the required cream concentration.
- Hygienic design: high-quality materials, polished plates, high-quality finishing of surfaces in contact with the product to avoid product deposits.
- Easy Drive: frequency converter for soft start and stop without friction clutch and with the lowest possible energy consumption, PLC for automatic separation and CIP sequencing control, operator panel for setting operating parameters and monitoring alarms.
- High quality cast iron bed plated with stainless steel.
- Assembled and tested design, easy to install and ready to go.
Principle of operation
Milk is fed into the drum, where it begins to rotate with it and, under the influence of centrifugal force, due to the difference in the densities of the components, is divided into fractions. The milk is fed into the space between the plates, where it separates into skimmed milk and cream, which move in opposite directions. Skimmed milk moves to the periphery and, bypassing the sludge space, is discharged under pressure using a pressure disk installed in the pressure chamber. A lighter liquid - cream moves towards the center, enters the pressure chamber, from where it is also discharged under pressure with the help of a pressure disk. The ratio can be adjusted using the valves on the outlets.
Standard equipment
- Frame Mounted Separator
- Control panel with PLC and operator panel
- Electric motor with converter
- Set of special tools and components for commissioning
- Operator's manual
Optional
- Standardization block
- Flow control accessories
- Feed water pumping station
- Product feed pump
- CIP system
materials
drum body | Stainless steel EN 1.4418 |
drum cover and piston | Duplex EN1.4462 |
Plates | AISI 316EN1.4401 |
Other surfaces in contact with the product | AISI 304EN1.4301 |
Casing and slurry tank | AISI 304EN1.4301 |
Separator bed | Cast iron lined with stainless steel |
Management cabinet | AISI 304EN1.4301 |
Frame | AISI 304EN1.4301 |
MAXCREAM 5T
TECHNICAL DETAILS | |
Maxcream 5T Separator | |
Capacity, degreasing (l/h) | up to 5000 |
Capacity, standardization (l/h) | up to 7000 |
Installed engine power (kW) | eleven |
Length x Width x Height (mm) | 1460x1700x1950 |
Can be used in | Milk skimming |
MAXCREAM 10T
TECHNICAL DETAILS | |
Maxcream 10T Separator | |
Capacity, degreasing (l/h) | Up to 10000 |
Capacity, standardization (l/h) | 12500 |
Installed engine power (kW) | fifteen |
Length x Width x Height (mm) | 1460x1700x1950 |
Can be used in | Milk skimming |
MAXCREAM 15T
TECHNICAL DETAILS | |
Maxcream 15T Separator | |
Capacity, degreasing (l/h) | Up to 15000 |
Capacity, standardization (l/h) | 13500 |
Installed engine power (kW) | 18.5 |
Length x Width x Height (mm) | 1460x1700x1950 |
Can be used in | Milk skimming |
MAXCREAM 20T
TECHNICAL DETAILS | |
Maxcream 20T Separator | |
Capacity, degreasing (l/h) | Up to 20000 |
Capacity, standardization (l/h) | 25000 |
Installed engine power (kW) | 22 |
Length x Width x Height (mm) | 1500x2400x2170 |
Can be used in | Milk skimming |
MAXCREAM 30T
TECHNICAL DETAILS | |
Maxcream 30T Separator | |
Maxcream 30T Separator | Up to 30000 |
Capacity, standardization (l/h) | 35000 |
Installed engine power (kW) | 37-45 |
Length x Width x Height (mm) | 1810 x 1950 x 2170 |
Can be used in | Milk skimming |